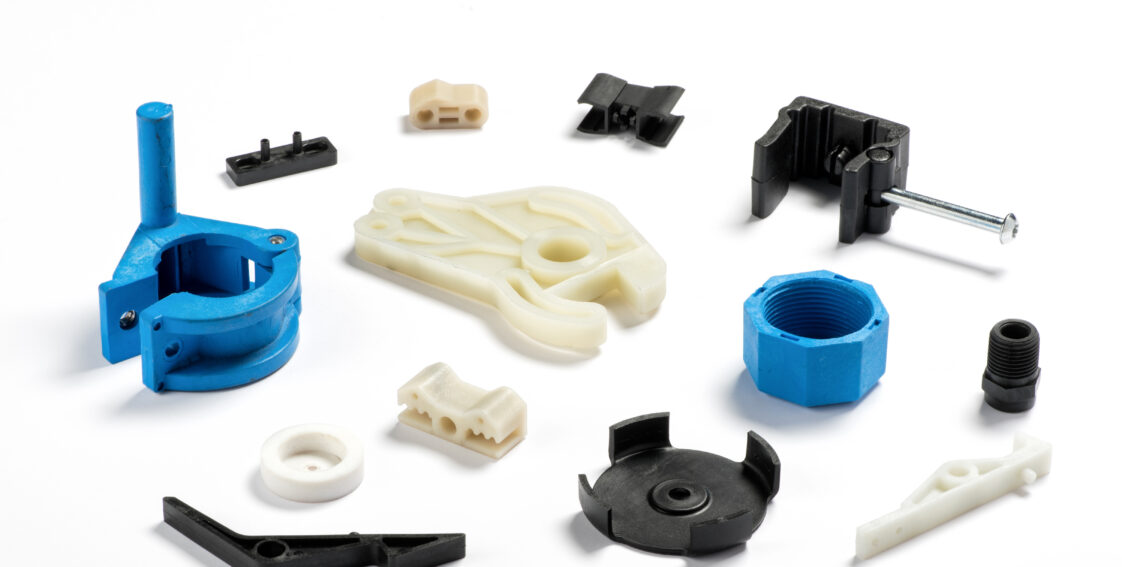
How Plastic Injection Molding Can Reduce Manufacturing Costs
Today’s manufacturers face a constant struggle to control ever-increasing costs. Environmental regulations, a growing emphasis on sustainability from customers and governments, labor shortages, and increasing material and fuel costs have manufacturers on their heels. Fortunately, plastic injection molding is one cost-effective solution more and more manufacturers are turning to.
Injection molding has quickly become the go-to resource for companies in multiple commercial and industrial markets who want to control costs, improve lead times, gain a competitive advantage, and improve profitability.
So, how can this process help reduce your manufacturing costs? Let’s take a closer look.
1. Offers Faster Turnaround Times
Companies are all-too-familiar with the consequences of missed deliveries, and these delays cascade throughout the supply chain as each member is forced to push their schedule out. While there are many reasons for delays, the most common include production errors, product defects, or out-of-tolerance parts.
Plastic molding removes these issues entirely. Repeatability is virtually guaranteed as each molded plastic part comes from the same mold (with the same part design). Speed is of the essence, as the time needed to mold a substrate or part (shot) is often measured in mere seconds. More importantly, molding machines can run 24/7, further reducing lead times.
Even with the initial time needed for tooling, mold design, and mold manufacturing, the turnaround time (TAT) for high-volume production runs of plastic molded parts is something other manufacturing processes cannot compete with. With many molds capable of producing up to one million shots before replacement, you’re guaranteed to have a consistent product time and again.
2. Reduces Material Costs
Global supply chain disruptions, increasing demand, transportation costs (fuel), and periodic shortages of critical metals and alloys drive up prices for manufacturers. These costs are only exacerbated when you consider the waste produced by some manufacturing processes where recycling or reusing the material is problematic.
Plastic injection molding can help you reduce material costs in the following ways:
- It reduces process waste: Injection molding is a closed-loop production process, so setup times are minimal. There are few process steps, and no time is wasted on long transit times moving parts from one workstation to another.
- Materials can be reused: While some unique thermoplastic resins can’t be recycled, far more can. Several resins, including polyethylene terephthalate (PET), high-density polyethylene (HDPE), and polypropylene (PP), can be reground and reused for other production runs.
- The upfront material costs are lower: Thermoplastic resins are generally cheaper than steel and other metals without sacrificing strength and durability. Current pricing for polypropylene is as low as $0.48 per pound, with low-density polyethylene (LDPE) and high-density polyethylene going for a low of $0.60 per pound. Additionally, a critical aspect of your mold’s design is ensuring your finished plastic part has the ideal wall thickness so you’re not using too much material.
3. Less Labor Is Required
Injection molding is the ideal solution for companies that don’t have enough labor or those struggling with high labor costs. Creating plastic molded parts is not a labor-intensive process. While the molding machines need to be monitored, most of the process is automated.
With fewer process steps, fewer employees are involved in the production process. The savings accrued can be increased by outsourcing your injection molding needs to a well-established plastic injection molding company.
4. It’s a Highly Repeatable Process
Repeatability is necessary for the automotive, aerospace, defense, transportation, and construction industries. For these industries (and many others), product quality is tied to public safety, so companies cannot be part of the supply chain if they cannot consistently mass-produce components that meet stringent quality standards.
The mold is the all-important insurance policy against product defects and errors. However, it’s critical that the mold is well-designed and comes from an established industry leader. Your plastic parts are only as good as the mold they come from and the company that designed the mold.
5. Shipping & Transportation
Multiple industries are following the lead of automotive and aerospace by using high-strength, durable, lightweight plastic parts to improve energy efficiency and reduce fuel consumption.
However, it’s not just about the weight of the material or its dimensions—it’s also about the size of the manufactured parts.
Freight is measured by a package’s actual or dimensional weight—whichever is greater. Metals like steel are provided in billet lengths of between 19.68 feet (6 meters) and 39.37 feet (12 meters) which only increases shipping costs because of the space they take up in a truck.
Plastic injection molding isn’t typically used to create large pieces, so the DIM weight for these components is low.
Learn More About the Cost-Saving Benefits of Plastic Injection Molding
Silver Basis Engineering is an award-winning, innovative manufacturer specializing in plastic injection molding and semi-solid die casting. Contact us today if you have questions about the benefits of plastic injection molding or want to learn more about our services and capabilities.